Penelope Font
Laser Cutting
Font Files
- Penelope.ttf
Font Details
Designer Name: | Nissa Studio |
Font License: | Free for Personal Use |
Website: | https://nissastudio.com/ |
Designers Note
This font is partial and free for PERSONAL USE only.
LINK TO PURCHASE COMMERSIAL LICENSE:
https://nissastudio.com/
follow my Behance for update my portfolio:
https://www.behance.net/nisasmart05f05
If there is something to ask please contact me:
[email protected]
to DONATE click here: https://www.paypal.me/NissaNana
I really appreciate your donations.
thank you
NissaStudio
LINK TO PURCHASE COMMERSIAL LICENSE:
https://nissastudio.com/
follow my Behance for update my portfolio:
https://www.behance.net/nisasmart05f05
If there is something to ask please contact me:
[email protected]
to DONATE click here: https://www.paypal.me/NissaNana
I really appreciate your donations.
thank you
NissaStudio
Character Map
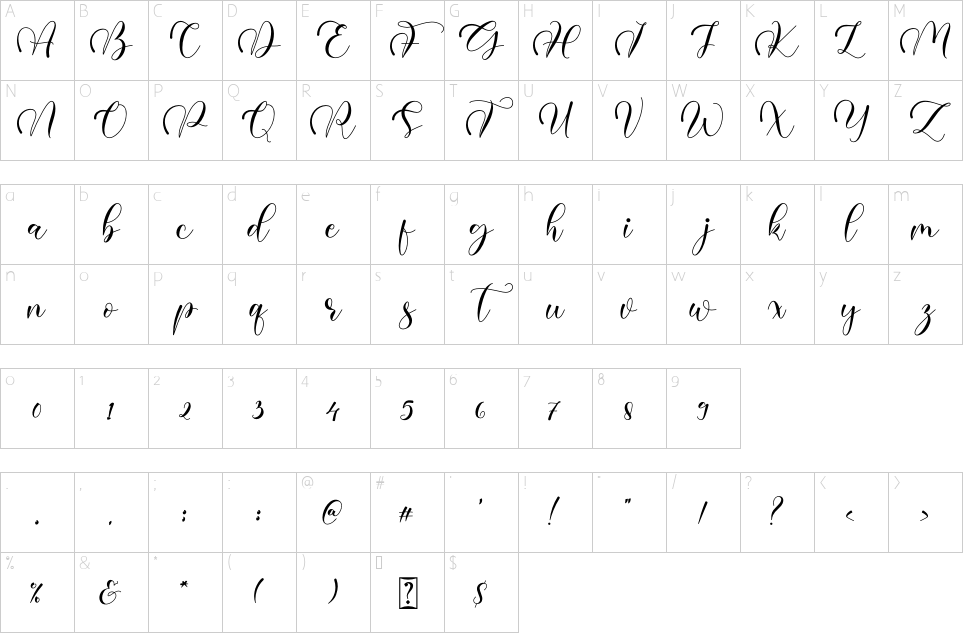