Organo Font
Laser Cutting
Font Files
- Organo.ttf
Font Details
Designer Name: | Nikola Nikolov |
Font License: | Free |
Website: |
Designers Note
This font is FREE. Please visit:
http://logomagazin.com/organo-font/
to see the colored Alphabet version of the font
For questions or proposals, feel very free to mail; [email protected]
http://logomagazin.com/organo-font/
to see the colored Alphabet version of the font
For questions or proposals, feel very free to mail; [email protected]
Character Map
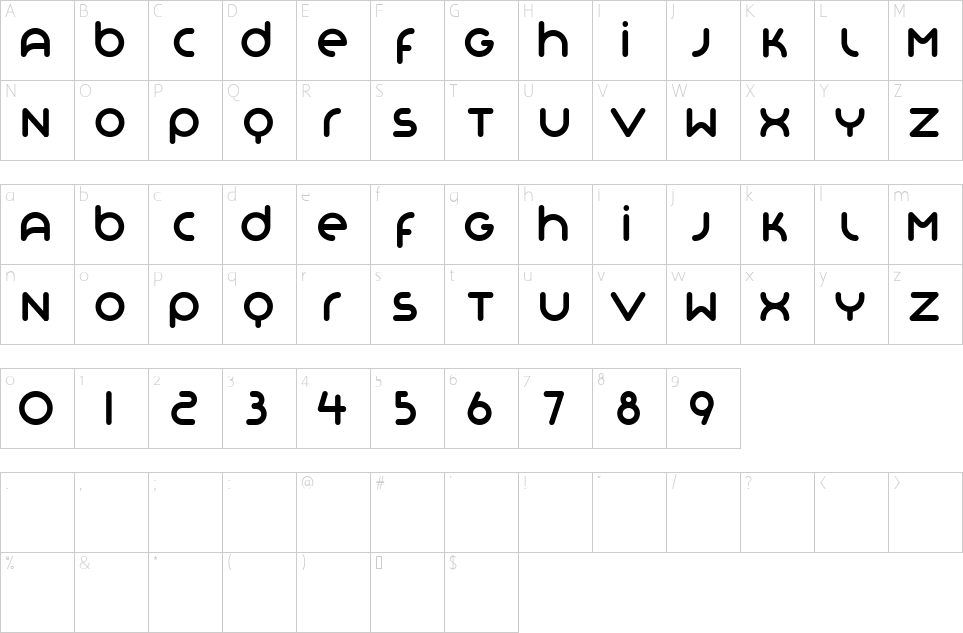